Maximizing Productivity with Advanced Rigid Stranding Techniques
Release time:
2025-05-27
Maximizing Productivity with Advanced Rigid Stranding Techniques Table of Contents Introduction to Rigid Stranding Techniques What is Rigid Stranding? The Importance of Maximizing Productivity in Manufacturing Benefits of Advanced Rigid Stranding Techniques Advanced Technologies in Rigid Stranding Best Practices for Implementing Rigid Stranding Techniques Case Studies and Success
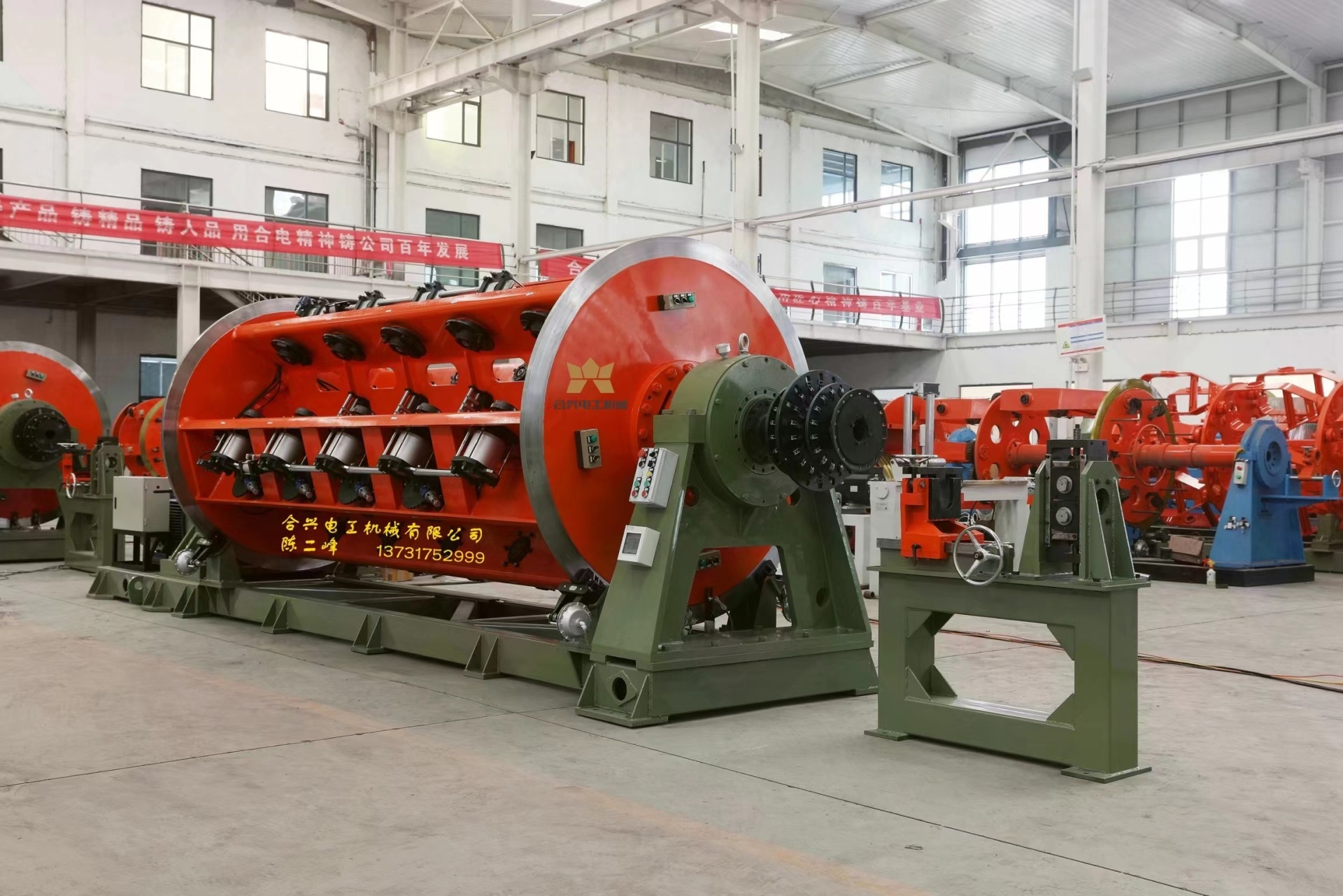
Maximizing Productivity with Advanced Rigid Stranding Techniques
Table of Contents
- Introduction to Rigid Stranding Techniques
- What is Rigid Stranding?
- The Importance of Maximizing Productivity in Manufacturing
- Benefits of Advanced Rigid Stranding Techniques
- Advanced Technologies in Rigid Stranding
- Best Practices for Implementing Rigid Stranding Techniques
- Case Studies and Success Stories
- Future Trends in Rigid Stranding Technologies
- Conclusion
- Frequently Asked Questions (FAQs)
Introduction to Rigid Stranding Techniques
In today’s fast-paced manufacturing environment, companies are continually seeking ways to enhance productivity and efficiency. **Advanced rigid stranding techniques** have emerged as a vital solution in the electrical and electronic products manufacturing sector. This article explores the intricacies of these techniques, highlighting their significance in maximizing productivity and offering insights into their implementation.
What is Rigid Stranding?
Rigid stranding refers to a specific method of forming and assembling wires into strands, used predominantly in the production of cables and conductors. This technique involves twisting multiple wires together in a precise configuration, which can improve both the mechanical strength and conductivity of the resulting cable. The process typically employs specialized machinery, such as **winding machines** and **stranding machines**, which automate the stranding process for high efficiency and consistency.
Key Characteristics of Rigid Stranding
- **Wire Arrangement**: In rigid stranding, wires are aligned in a predetermined pattern that optimizes performance.
- **Twisting**: The wires are twisted at specific angles to reduce the risk of interference and signal loss.
- **Coating**: Often, wires are coated with materials that enhance durability and conductivity.
The Importance of Maximizing Productivity in Manufacturing
In the competitive landscape of the electrical and electronic manufacturing industry, **maximizing productivity** is essential for several reasons:
1. **Cost Efficiency**: Increased productivity leads to lower production costs, allowing companies to offer competitive pricing.
2. **Quality Control**: Efficient processes typically yield higher-quality products with fewer defects.
3. **Market Demand**: In a market driven by consumer demand, faster production rates can lead to better customer satisfaction and loyalty.
4. **Sustainability**: Enhanced productivity can also contribute to more sustainable manufacturing practices by minimizing waste and energy consumption.
Benefits of Advanced Rigid Stranding Techniques
Implementing advanced rigid stranding techniques offers numerous benefits that directly contribute to productivity:
Enhanced Mechanical Strength
By twisting wires together, rigid stranding increases the mechanical strength of the final product. This is particularly important in high-stress environments where cables may face significant wear and tear.
Improved Electrical Conductivity
The precise arrangement and twisting of wires can enhance electrical conductivity. This improvement is critical in applications where signal clarity and strength are paramount.
Increased Production Speed
With the advent of modern stranding machines, manufacturers can significantly reduce the time required to produce strands. Faster production translates to increased throughput.
Cost Reduction
Advanced techniques help minimize material waste and reduce labor costs. Efficiency gains in production lead to lower overall costs, boosting profit margins.
Advanced Technologies in Rigid Stranding
The evolution of stranding machines has played a pivotal role in enhancing productivity. Key technologies include:
Automated Stranding Machines
These machines allow for precise control over the stranding process, ensuring uniform tension and alignment of wires. Automation reduces the chance of human error and increases output rates.
Computer-Aided Design (CAD) Systems
CAD systems are used to plan and design stranding patterns before production. This simulation capability helps manufacturers optimize designs and reduce trial-and-error during the actual stranding process.
Real-Time Monitoring and Quality Control Systems
Implementing real-time monitoring systems enables manufacturers to detect issues early, ensuring that any deviations from quality standards are addressed immediately. This proactive approach leads to higher quality outputs.
Best Practices for Implementing Rigid Stranding Techniques
To fully leverage the benefits of rigid stranding techniques, manufacturers should consider the following best practices:
Comprehensive Training
Investing in training programs for staff ensures that employees are familiar with the latest technologies and best practices in rigid stranding.
Regular Maintenance of Equipment
Maintaining stranding machines and related equipment is crucial to avoid downtime and ensure optimal operation.
Continuous Improvement Process
Establishing a culture of continuous improvement encourages teams to regularly assess processes and seek out efficiencies.
Data-Driven Decision Making
Utilizing data analytics can help identify trends, inefficiencies, and areas for enhancement in the stranding process.
Case Studies and Success Stories
Several companies have effectively implemented advanced rigid stranding techniques to maximize productivity:
Case Study 1: Electrical Cable Manufacturer
A leading electrical cable manufacturer adopted automated rigid stranding machines, resulting in a 30% increase in production speed and a notable reduction in material waste. The company reported substantial cost savings and improved product quality.
Case Study 2: Automotive Wiring Solutions
An automotive wiring manufacturer implemented real-time monitoring systems to track production quality. This initiative led to a significant decrease in defects and an increase in customer satisfaction ratings.
Future Trends in Rigid Stranding Technologies
As technology continues to evolve, so too will the methods used in rigid stranding. Some anticipated trends include:
Integration of AI and Machine Learning
AI and machine learning technologies will likely improve the efficiency of stranding processes by optimizing designs and predicting maintenance needs.
Sustainability and Eco-Friendly Practices
Future developments will focus on producing sustainable materials and minimizing the environmental impact of manufacturing processes.
Enhanced Customization Capabilities
As customer demands diversify, manufacturers will increasingly look to provide customized stranding solutions that cater to specific industry needs.
Conclusion
Utilizing advanced rigid stranding techniques is essential for manufacturers aiming to maximize productivity in the electrical and electronic products sector. By embracing new technologies, optimizing processes, and adhering to best practices, companies can achieve significant improvements in efficiency, quality, and cost-effectiveness. As the industry evolves, staying ahead of trends will ensure that manufacturers remain competitive in a rapidly changing marketplace.
Frequently Asked Questions (FAQs)
What are the key advantages of rigid stranding compared to other stranding methods?
Rigid stranding offers enhanced mechanical strength, improved electrical conductivity, faster production speeds, and reduced costs, making it ideal for high-performance applications.
How can manufacturers ensure consistent quality in rigid stranding processes?
Implementing real-time monitoring systems and regular maintenance of stranding equipment can help ensure consistent quality throughout the production process.
What kind of training is necessary for staff involved in rigid stranding?
Staff should receive training focused on machine operation, quality control procedures, and the latest advancements in stranding technologies.
Are there specific industries that benefit most from rigid stranding techniques?
Industries such as automotive, telecommunications, and power generation significantly benefit from the use of rigid stranding techniques due to their need for high-quality cables and conductors.
What is the future of rigid stranding technology?
The future will likely see the integration of AI, a focus on sustainability, and enhanced customization capabilities to meet evolving market demands.
TAG:
Recommend News
HEXING CABLE MACHINERY
TEL: +86-317-3601666, +86-317-3236119
FAX: +86-317-3618408
E-MAIL: china@hbhxdg.cn
E-MAIL: hbhxdg@gmail.com
WEB: http://www.hbhxdg.cn
ADD: Baoantun Industrial Zone, Hejian City, Hebei Province